「プレス安全作業の盲点」
(株)小森安全機研究所 山田輝夫(山田労働安全コンサルタンと事務所代表)
筆者がプレス業界にかかわり始めたのは197.4年からで、オイルショックに巻き込まれ、混沌とした社会であった。現在、その当時では考えられなかったような技術革新、経済のグローバル化。雇用形態の変化が起き。多種多様な社会になっている。 30数年が経過し、さまざまなプレス災害を聞いたり目撃し、現場検証した経緯の中で、なぜ起きてしまうのだろうか、防げなかったのか、利便性ばかりでなく、もっとプレス機械作業の危険性を伝えておかなければならなかったのではないのか、そんな思いが残っている。 近年、統計的に、はプレス災害の死傷者数は減少しているが、ここ数年、指の切断者を伴う被災者数は増加傾向にある。プレス機械の構造規格などが78年に告示され、災害防止のため、さまざまな安全啓蒙活動が行われてきた。厚生労働省は99年に、労働安全術生マネジメントシステム、01年に機械の包括的な安全基準を通達し、またILO(世界労働機構)も01年に労働安全衛生マネジメントシステムのガイドラインを発表し、安全管理啓蒙活動のグローバル化を推進している。さらに、昨年、安全衛生法の改定が行われ、リスクアセスメントの取組みがいよいよ本格的に行われようとしている。また、国際安全規格のJIS規格への導入も進み、さまざまな方而で安全の見直しが始まり、プレス機械などの構造規格の見直しも行われようとしている。 そこで、筆者が在籍した30数年間の安全活動を迦じ、経験したさまざまな災害事例を基に、なぜ起きてしまったのか、何が問題なのか、作業中の盲点となってしまう状況を検証してみたい。そして、そのことが今後の安全啓蒙活動の参考となれば幸いである。
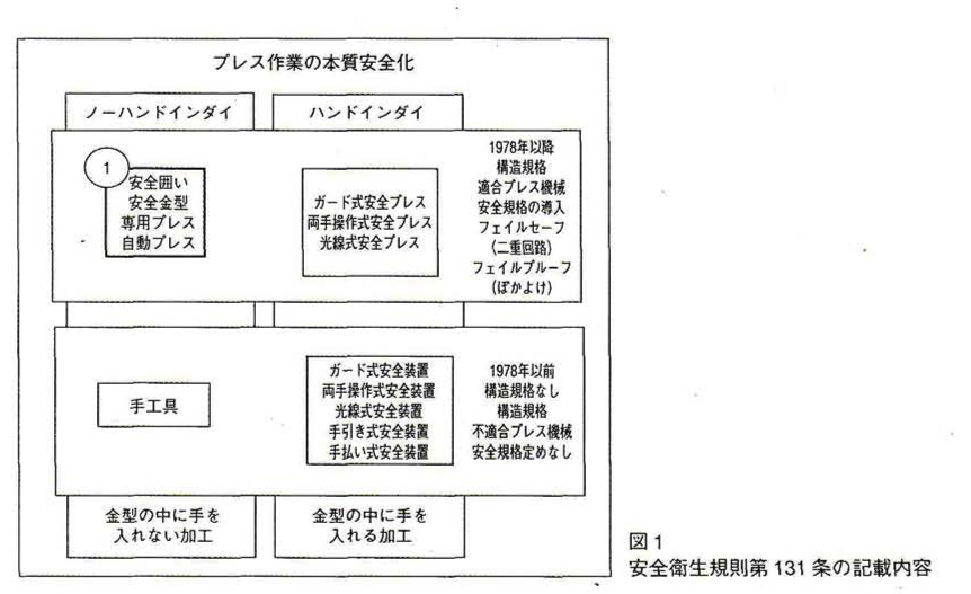
プレス作業における安全とは
プレス作業の安全とは本質安全をめざすことである。しかし、その中身を解釈するには難しい専門用語の解釈が必要である。図1で簡単に、安全衛生規則第131条に記載されている内容を紐解くと、本質安全とは①の内容である、安全囲い、安全金型、専用プレス、自動プレスを採用することである。中でも、安全囲い、安全金型、専用プレスは作業する上でそれぞれ8mm以下の隙間にして指先も入らないようにすることである。自動プレスとは。送り装置などを使用した加工が法である。
一般的に、プレス作業は大きく分けて2種類に区分けされる。ハンド・イン・ダイと呼ばれる金型内に手をいれて行う加工方法と、ノーハンド・イン・ダイと呼ばれる金型内に手を入れないで行う加工方法である。通常現場で行っている作業で比較すると、ハンド・イン・ダイとは手作業であり、ノーハンド・イン・ダイとは自動化されたものである。自動化は生産性の向上に寄与するが安全性からみても重要な意味がある。しかし、自動化したから安全ではなく、思わぬところに災害を引起こす要因も持っている。その理由に金型の段取り、トラブル処理のため、金型内に手を入れ被災して・しまうことが挙げられる。
78年以降製造されたプレス機械はプレス構造規格の要求があり、安全なプレス機械の使用を義務付けしているにもかかわらず、災轡が後を絶たない。これにはいくつかの理由がある。事業者、プレス機械作業者それぞれにプレス機械を使用する上で危険なこと、安全であることを深く理解していたのだろうか。しかし実際には「不注意であった」「うっかりしていた」など、結果的に本人の責任にしていることが多い。またプレス作業をする上で安全上の思わぬ盲点七なっている状況も少なくない。
それに図1のように78年以前に製造されたプレス機械がいまだに現役として使川されており、プレス機械の種類、構造、加上方法などにより、さまざまな安全対策が考えられているが、その安全対策の難しさもあり、なかなか進まないのが現状である。さらに、H本ではそれらの安全対策は、人に委ねられているケースが多く、その割には、人はミスを犯すというヒューマンエラーの考えが作業者、事業者にあまりないことも事実である。
今回は特に、小型機のCフレームフリクションプレス機械を中心に安全装置を設置、使用していたにもかかわらず、災害に巻き込まれてしまったプレス安全作業の盲点となった状況を検証してみる。
プレス安全作業の盲点
現在のプレス機械の構造規格ではガード式安全装置、両手操作式安全装置、光線式安全装置の3種類の安全プレスがある。しかし、それらが単独で使用されるプレス機械はあまりなく、ほとんどが両手操作式安全装世と光線式安全装吐または、両手操作式安全装置とガード式安全装置併用で使われている。その中でも両手操作式安全装置と光線式安全装置の併用で使われているものが最も多い。そこでこの両手、光線式安全装置併用のプレス機械を使用し、プレス作業の盲点となってしまった状況を考える。
両手操作式の安全装置は通常、図2のような構成になっていて、押ボタンの間隔は300 mm 以上である。なぜ300 mm なのか。これは片手の親指と小指で押せない距離である。それ以上に国際安全規格では厳しく、肘と手が使えない距離550mm以上となっている。押ボタンスイッチは再起動防止回路や、接点溶着を考え、A接点、B接点の構成になっている。B接点とは常時電気が流れている状態で、押ボタンを押すと接点が開放され、電気が流れなくなる。A接点とは通常は電気が流れていない状態で、押ボタンを押すと接点がつながり電気が鳫れる。これらの接点は、接点不良、接点溶着を起こすことが考えられる。万一、接点溶着を起こしても、機械的に強制切断できるように非常停止などの接点はB接点で使用しなければならない。両手操作式安全装置のー工程一停止、再起動防止は次に記述した作業を行うことでその安全を確認できる。
・第1に片手では絶対動かない。
・第2に下死点手前までは、押ボタンを離したら必ず止まる。(安全一工程)
・第3に両手を押したままでも必ず上死点で止まる。(一工程一停止)
・第4に第3の状態で、片手を離し、再度押しても動かないこと。(再起動防止)
これらの一連の動作の中で第2の下死点手前の位置が問題となる。
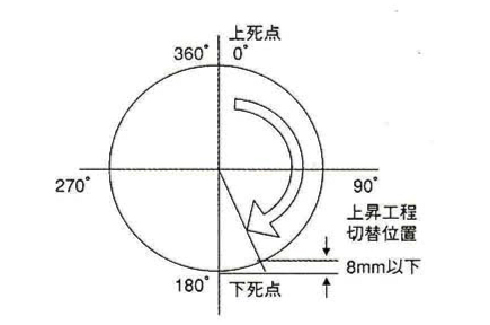
上昇無効回路が安全一工程とともに組み込まれており、通常、図3のように角度指示計で170°付近で、手を離してもそのまま上死点で止まるようになっている。ただ、ここで注意しなければならないことがある。手を離す位置である。上昇工程への切替位置は金型の上型と下型の隙間を8mm以下とすべきである。この位置が8mm以上の位置、角度指示計の150°とか120°だったりすると、金型の上型、下型の間がストローク長さにもよ‘るが大きな空問ができ、押ボタンを離し、製品の位置直しなどを行おうとして手を入れ、被災してしまうことが十分考えられる。したがって、これらのことも日常点検に組み入れて、毎日確認する必要がある。
そのほか、日本国内では明確な規定になっていないが、国際安金規格ではこの両手抑ボタンスイッチを0.5秒以内に同時に押さなければ起動しないようになっている。作業する上でほとんどこのことは意識していないと考えられる。
次に図2で示したように、押ボタンはガードリングより低くなっている。そして、ガードリングは操作盤に固定され、取外しはできないようになっている。図のように押ボタンとガードリングの問には2~5mmの隙間がなければならない。ごみ、異物、油などが入らないようにゴムカバーで覆われていて、見えにくいから注意を必要とする、このような複雑な規定、構造になっているにもかかわらず、押ボタンの上にウレタンゴムなどをあてがい手押し作業をしている状態を見かける。、これは非常に危険である。押ボタンの位置が高くな
っていると身体の一部が触れただけでも起動してしまう。このことが原因で大きな災害になった事例もある。作業をしていると指が疲れ、作業性が悪いとのことで、何も知らない作業者が簡単に行ってしまう初歩的なミスである。このガードリングはフェイルセーフ機構といわれ、安全作業をする上で重要な意味を持っている。カシメ、組立てなどの小型プレスを社内で製作する場合を見かけるが、プレス機械は自動ラインであっても押ボタンにはガードリングが必要である。プレス構造規格第45条に細かく記載されている。
2.光線式安全装置の盲点
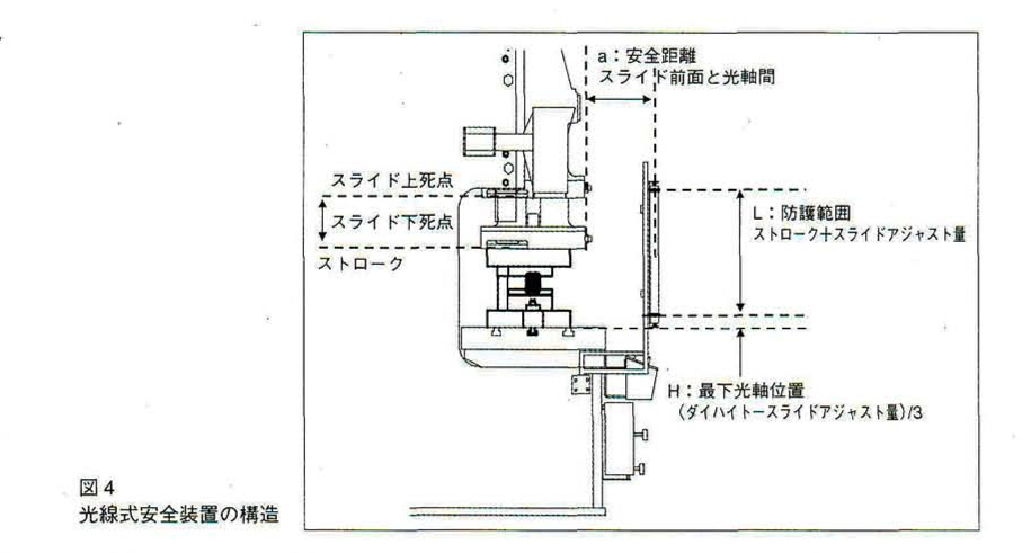
光線式安全装置(図4)は、‘急停止機構を持つプレス機械によく使われている。しかし、その構造よりも、なぜこの位置に設置されているのか、その理山を知っておく必要がある。両手操作式安全装置は両手を使って自分の意志で押して起動させることと比べて、光線式安全装置は光線が働き監視してもらっていることを実感できるためか、安心してしまうようである。なおかつ光線が目、に見えないために、思いもよらぬ災害が発生してしまうことがある。加えて、光線式安全装置の安全距離不足が原因でけがをしてしまうことや、プレス機械の特定自主検査(1年に1回以上)の結果報告でも安全距離不足が指摘されているケースが
多い。 、
光線式安全装置の安全距離、防護範囲、最下光軸位置などプレス安全装置の専門用語の内容をよく理解しておくことが大切である。安全管理の上でも光線式安全装置を有効にして使用することや、キーの保管などとともに、プレス機械作業主任者に課せられた重要な職務のlつになっている。
最大停止時間とは両手押ボタンを離してスライドが停止するまでの時問である。通常、電気的な停止時間(リレー接点などの通電時間)と機械的な停止時間(バルブ、ブレーキが作動し。スライドが止まるまでの機械的な動作時間)の合計となっている。プレス機械の仕様銘板にこの値が記職されている。光線式安全装置の安全距離(a)はこの最大停止時間に人の手の動作時問1.6 m/sを掛け算した数値である。計算された安全距離以上に離れていないと、光線を遮ってからプレスのスライドが停止する前に手が金型に入り、被災してしまうことになるきわめて重要な意味をもつ数値である。
防護範囲(L)はプレス機械のストローク長さ、にスライドアジャストX11を加えた艮さ以上を防護 しなければならない。しかしこれもこの数値の防 汲範囲だけでは不十分である。小型機では100mmにも満たないものがある。安全装置の上側からの手の侵入は十分考えられる。迦常Cフレームの最小の防護は400mm以上となっている。安全規格では光軸ピッチは50mmとなっているが20~25 mmのものが使われている。国際安全規格ではこの光軸ピッチにも細かな規定が定められていて、7.5 mmピッチのものもあり、指先も入らないようになっている。
最下光軸位置とは光線式安全装置の一番下にある光軸である。問題はその光軸位置がホルスター上面から、どれくらい離れた取付位置になっているかである。安全規格ではこの取付高さ(H)はダイハイトースライドアジャスト量の1/3以下の距離でなければならないと決められている。この光軸の取付位置は、一般的に金型のダイの上面の位世(加工面)より下になければならない数値である。作業性が悪いといって光軸の位置を高くすると、手が金型内に入っても光線を遮斷できず、検出できなくなってしまう。以上のように馴|かな規格が決められており、なおかつ安全装世の取付位置は変更できないようにノックピンで固定され
ている。しかし、両手操作式、光線式安全装置併用のプレス機械を使用し、安全であるはずにもかかわらず、両手を被災してしまった盲点となった状況を検証してみる。小型のプレス機械では図5の写良で見られるような川り作業を見かける。
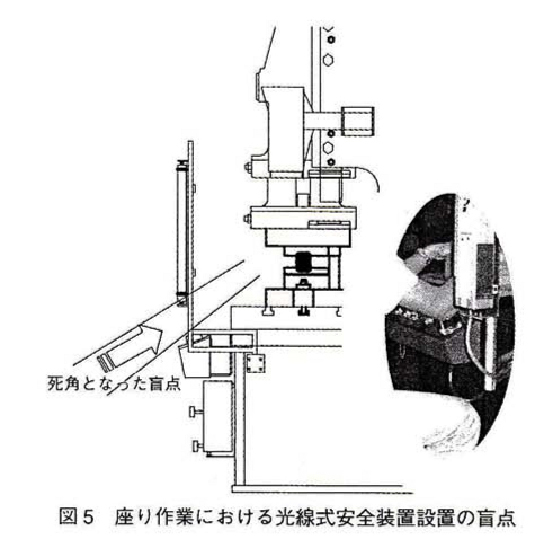
この状況をよく見てみると、光線式安全装置の設置は規格を満たしてい、たにもかかわらず、両手が最下光軸位置よりも下輒から金型内に入ってしまったと考えられる。そして悪いことに偶然、その状態で両肘で押ボタンが押されたのではないかと考えられる。実際に調査中、何回か意識して行ってみるとスライドが起動してしまった。偶然とはいえ、両肘で同一に0.5秒以内に押すことはかなり意識して行わないとできない。これは不注意ではなく、安全装置と作業性のミスマッチといえる。通常、プレス作業は立って作業をすることを一般的に考えているので、特に、組立て、カシメなどの座り作業が多い小刑プレス機械では、光線式安企装吐の最下光軸位置をホルスター上面より低い位置に設置しておくことが安全上重要である。それに加えて、前述した両手押ボタンの同時起動を0.5秒以内としておけば防げた災害である。外見上の判断ばかりではなく、用語の持つ内容を理解し、それぞれの安全距離を常に確認する必要がある。
3.自動化ラインの盲点
6)。
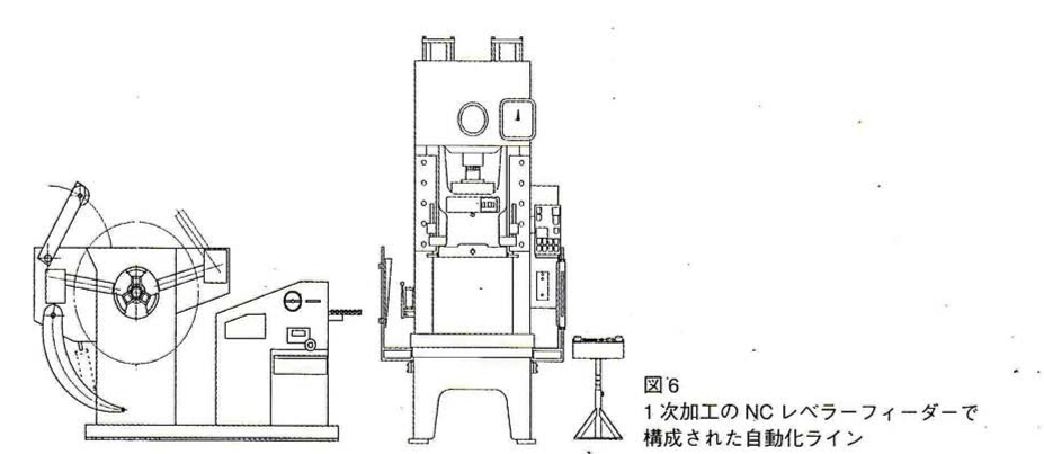
それと各周辺装置が主になり、フィードマスター方式と呼ばれ、プレス機械に起動信号を出
し連助して助くロボット、トランスフアなどを使用する2次加工がある。特に問題となるのはフィードマスター方式で、ロボットなどを使用した場合で、起動条件が規定されるが、プレス機械の運転は実際は周辺装置のスタート信号で動作しているのである。周辺装置のロボットなどが主体となっていて、特に起動信号が出力されているにもかかわらず止まっている 場合は危険である。プレス機械と周辺装置のインターロック、非常停止の位置、急停止回路の取り方など十分検討しなければならない。数台で構成される自動化ラインは、プレス機械そのものより全体的なシステムとしての安全管理が必要になる。
周辺装置も安全榾を設け、危険な状況へ人が椄近しないようにしなければならない。大型設備になればなるほど危険度は増してくるので、周辺の安全対策も見落とせず、注意が必要である。図6は一般的な1次加工のNCレベラーフィーダーで構成された自動化ラインである。コイル材の扱いは板厚が厚くなるほど自由がきかないので、装置に備えられている補助具を有効に活用することである。
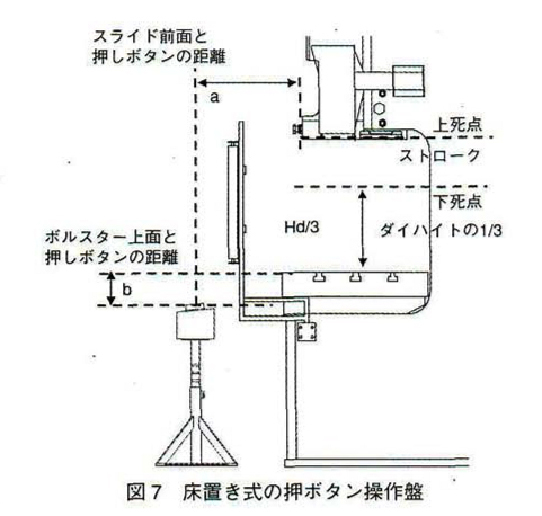
そのほか、押ボタン操作が直接プレス機械についていない床置き式の押ボタン操作盤(図7)、がある。これも前述の両手操作式安全装置の押ボタン同様、安全距離は計算式に基づかなければならない。移動できる操作盤はプレスの前面ではなく製品の取出し側に置かれ、、安全装置の外側から手が入ってしまうことが考えられる。したがって、プレスの左右両側にもガードなどの安全対策が必要である。また、複数人の操作となる大型プレスの自動化ラインは、さらにプレス機械の回りに、作業者の注意が行き届かない死角となるところが出てくる。大型設備はこれらの対処にガード、榾を設け、人が入れないような領域的な分離による
安全対策をする方法と、人がいることを検知できるようなエリアセンサなどで、機械が動かないようにする時間的な分離による安全対策がある。職場の作業状況に合わせて選定すべきだろう。
☆ ☆
安全に対する見方、考え方は大きな転換期にきている。特にプレス作業のリスクを考えると、機械の構造上の問題、作業者の問題、作業情報の問題、安全管理の問題などを加味して考えなければならない。
まず、機械構造上の問題点としてフレーム形式、クラッチ形式、10 kN にも満たない小型機から、10000 kN を越す大型機械までさまざまなプレス機械がある。そのための安全対策も千差万別で、これでいいというものがない。現場での対応が求められる。そのため、何か危険で、その安全対策はどうすればよいのか、プレス機械の構造の理解まで今後必要になってくる。
次に作業者の問題点として、誰しもが自分はミスをしないと思っている。本質安全が進むと機械側に安全を託してしまう傾向がある。残念ながら、人はヒューマンエラーを避けられない。このことは作業者自身も知っておかなければならない。また、高齢社会になり、工場内のバリアフリーなど加齢の問題の早急な解決も求められる。
そして、作業情報の問題点として、プレス加工の裾野は広く、さまざまな分野で行われている。技術革新のスピードは速く、生産性は飛躍的に向上し、サーボプレス、複合加工、新素材など知らなければならない要素は多い。危険性がどこにあるのか、その対策はどんなものがあるのか、加工技術、加工方法などの作業にかかわる情報を的確に作業者は知っておく必要がある。
さらに、安全管理の問題点として、現在、国際安全基準のJIS規格への取組み、労働安全衛生マネジメントシステムの取組みなどが行われているが、安全基準、運用、点検、見直しなどを行うプレス作業主任者には、なお一層の管理としての業務の質を向上させなければならない。特にプレス現場におけるリスクアセスメントを行う場合、作業主任者が中心となって自主的に巡めなければならないからである。
![]() |
---|
プレス技術 |
「レーザーを使った新方式のセーフティーデバイス」 |