「プレス作業の安全対策」
(株)小森安全機研究所 小森雅裕
プレス災害の発生状況
プレス機械の安全対策がわが国で本格的に開始されたのは、昭和30年代であった。戦後から機械産業の黎明期にあり。安全作業より能率重視のプレス作業が中心で休業8日以上のプレス災害は2万件程度発生していた。プレス加工業界では「指の1本や2本落とさなければ一人前とは言えない」と言われたほどプレスの災害は非常に多かった。当時の対策は、プレス機械の人部分がポジティブクラッチ式であったことから、このプレスに適合する両手起動式などの安全装置や、作業に危害を及ぼさない金型の構造等について検討が進められた。プレス機械には安全装置がほとんど取り付けられていなかったので、様々なものが考案され、効果を発揮した。
その後、昭和4O年代からは、自動車産業の台頭によりプレス機械関係の産業は大きな飛躍を遂げる時期に入り、プレスの設置台数も増加するが、それに従ってて災害も多発し、休業4日以上のプレス災害は1万件程度発生した。昭和40年代後半から50年代の初頭にかけて、設備安全対策の重点は、自動化や安全プレスの普及促進などにおかれ、厳しい行政指導と相まって災害はさらに減少傾向に向かっていった。
昭和47年の労働安全衛生法の施行に伴い、ノーハンドインダイの原則が労働安全衛生規則第131条に盛り込まれたことや、昭和52年に改定された動力プレス機械構造規格に安企プレスの考え方が盛り込まれた影響が大きい。プレスの特定自主検査も制度化され、機械を安全に維持管理する面からも対策が図られた。ポジティブクラッチ付きのプレスが全体の7割以上を占めていたものが、急停止機構を備えるフリクションクラッチ付きのプレスに入れ替えられ、小型のプレスから中型のプレスに移行して、急停止機構の装備により災害が人幅に減少していったと考えられる。
昭和48年には10,365件あった災害は、10年後の昭和58年には5,968件と40%の減少がみられ、さらに10年後の平成5年には2,665件と50%の減少率になった。昭和48年と平成5年を比較すると7,700件も減少している。昭和50年代の画期的な対策の導入によってプレス機械による労働災害は激減したが、昭和60年代中頃から平成に入ると下げ止まりの傾向に入ってしまった。最近の災害発生状況では、平成12年1,407件から平成16年1,121件と推移している(図1)。これは下げ止まりというより増加に転じていると考えなければならない。かなり深刻な問題である。発生原因の詳細についての分析が必要であるが、景気の復活に伴い実際の感覚としても、プレス災害は増加に転じていると感じられる。
未曾有の不況の中で勝ち残った製造業のの高付加価値生産の中では、従来までのノーハンドインダイや安全プレスの設置等の対策は一通り行き渡り、文字どおり在来型の対策では防ぎきれないプレス災害が多発しているのではないだろうか? プレス機械のの種類も旧式のポジティブクラッチ式のプレスはどんどん減少し、急停止機構を備えるフリクションクラッチのプレスが増加している中で、必ずしも災害が著しく減少しないのは、急停止機構がついていれば安全であるとする従来の考え方が通用しなくなったことを意味している。確かにポジティブクラッチ式に比較すれば急停止できることが安全上は大きな優位性につながるが、それだけでは災害減少という結果は簡単には出てこない。フリクションクラッチのプレスが増えれば、災害も増加してしまうのである。手を金型の中に入れないという本質安全対策はもちろん重要であり推進させなければならないが、すべてのプレス作業にこれを対応させることはきわめて困難である。プレス安全対策の具体的展開は、ハードウェア面だけでなく、個々の作業内容を十分に検討し、それぞれの作業ごとに丁寧に対策を具備させていかなければならないというソフトウェア面の検討が重要なのである。すべてのプレス作業にノーハンドインダイや安全プレスを使用することはできないし、設備や対策が難しい作業には、作業の分析が必要であり、きめ細かな作業標準が要求されてくる。
リスクアセスメントにより危険有害要因の特定や災害防止対策を積極的に展開しなければならないゆえんである。今般、労働安全衛生法が改正され、リスクアセスメントが努力義務化されたので、プレス事業場での具体的展開が急務となってきた。全産業で3,200件を超えると言われる指の切断事故が多発していることが明白なので、リスクアセスメント・機械の包括的な安全基準に関する指針の取り扱いが従来にも増して重要になってきた。ここでは、リスクアセスメントの具体的手順などの詳説はできないが、具体的な方法論については。中災防と日本金属プレスエ業協会および関係者の協力により、初めてリスクアセスメントに取り組む中小規模のプレス事業場向けに検討が進められ、本年度末までには報告書が完成するようなので、大いに参考にして実行を図らなければならない。包括指針の実施状況などの実態調査や実務展開などの行政の動きが活発になるように聞いており、プレス災害の増加傾向に歯止めがかかることが期待される。
また、製造業のプレス機械による死亡災害の推移(表1)を見ると、平成15年以外は毎年数名がプレス機械で亡くなっており、大きな問題となっている。非定常作業での災害が多く見られるが、大型プレスやターレットパンチプレスでの被災も多い。プレス機械により毎年死亡災害が発生していることに対して、今後も真剣に対応していかなければならない。ここにおいても機械の包括安全基準の導入がきわめて重要になることは言うまでもない。
スライドによる危険の防止だけではなく。プレスに関連する金型や材料の運搬作業から部品の搬出までの過程の中で、それぞれに安全を最後先にする考え方が重要になってくる。すぐにでもプレス機械に起因する死亡災害はゼロにしなくてはならない。安全措置の方法も構造規格に要求されるレベルから先取りした安全措置が必要である。その意味で欧州規格の導入はきわめて効果的であると思われる。
その後、昭和4O年代からは、自動車産業の台頭によりプレス機械関係の産業は大きな飛躍を遂げる時期に入り、プレスの設置台数も増加するが、それに従ってて災害も多発し、休業4日以上のプレス災害は1万件程度発生した。昭和40年代後半から50年代の初頭にかけて、設備安全対策の重点は、自動化や安全プレスの普及促進などにおかれ、厳しい行政指導と相まって災害はさらに減少傾向に向かっていった。
昭和47年の労働安全衛生法の施行に伴い、ノーハンドインダイの原則が労働安全衛生規則第131条に盛り込まれたことや、昭和52年に改定された動力プレス機械構造規格に安企プレスの考え方が盛り込まれた影響が大きい。プレスの特定自主検査も制度化され、機械を安全に維持管理する面からも対策が図られた。ポジティブクラッチ付きのプレスが全体の7割以上を占めていたものが、急停止機構を備えるフリクションクラッチ付きのプレスに入れ替えられ、小型のプレスから中型のプレスに移行して、急停止機構の装備により災害が人幅に減少していったと考えられる。
昭和48年には10,365件あった災害は、10年後の昭和58年には5,968件と40%の減少がみられ、さらに10年後の平成5年には2,665件と50%の減少率になった。昭和48年と平成5年を比較すると7,700件も減少している。昭和50年代の画期的な対策の導入によってプレス機械による労働災害は激減したが、昭和60年代中頃から平成に入ると下げ止まりの傾向に入ってしまった。最近の災害発生状況では、平成12年1,407件から平成16年1,121件と推移している(図1)。これは下げ止まりというより増加に転じていると考えなければならない。かなり深刻な問題である。発生原因の詳細についての分析が必要であるが、景気の復活に伴い実際の感覚としても、プレス災害は増加に転じていると感じられる。
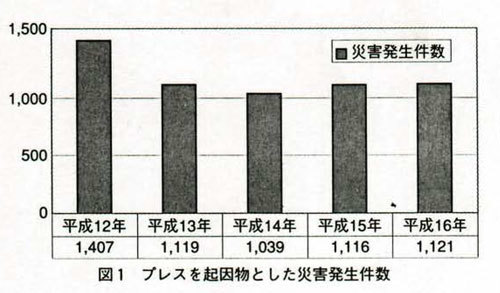
未曾有の不況の中で勝ち残った製造業のの高付加価値生産の中では、従来までのノーハンドインダイや安全プレスの設置等の対策は一通り行き渡り、文字どおり在来型の対策では防ぎきれないプレス災害が多発しているのではないだろうか? プレス機械のの種類も旧式のポジティブクラッチ式のプレスはどんどん減少し、急停止機構を備えるフリクションクラッチのプレスが増加している中で、必ずしも災害が著しく減少しないのは、急停止機構がついていれば安全であるとする従来の考え方が通用しなくなったことを意味している。確かにポジティブクラッチ式に比較すれば急停止できることが安全上は大きな優位性につながるが、それだけでは災害減少という結果は簡単には出てこない。フリクションクラッチのプレスが増えれば、災害も増加してしまうのである。手を金型の中に入れないという本質安全対策はもちろん重要であり推進させなければならないが、すべてのプレス作業にこれを対応させることはきわめて困難である。プレス安全対策の具体的展開は、ハードウェア面だけでなく、個々の作業内容を十分に検討し、それぞれの作業ごとに丁寧に対策を具備させていかなければならないというソフトウェア面の検討が重要なのである。すべてのプレス作業にノーハンドインダイや安全プレスを使用することはできないし、設備や対策が難しい作業には、作業の分析が必要であり、きめ細かな作業標準が要求されてくる。
リスクアセスメントにより危険有害要因の特定や災害防止対策を積極的に展開しなければならないゆえんである。今般、労働安全衛生法が改正され、リスクアセスメントが努力義務化されたので、プレス事業場での具体的展開が急務となってきた。全産業で3,200件を超えると言われる指の切断事故が多発していることが明白なので、リスクアセスメント・機械の包括的な安全基準に関する指針の取り扱いが従来にも増して重要になってきた。ここでは、リスクアセスメントの具体的手順などの詳説はできないが、具体的な方法論については。中災防と日本金属プレスエ業協会および関係者の協力により、初めてリスクアセスメントに取り組む中小規模のプレス事業場向けに検討が進められ、本年度末までには報告書が完成するようなので、大いに参考にして実行を図らなければならない。包括指針の実施状況などの実態調査や実務展開などの行政の動きが活発になるように聞いており、プレス災害の増加傾向に歯止めがかかることが期待される。
また、製造業のプレス機械による死亡災害の推移(表1)を見ると、平成15年以外は毎年数名がプレス機械で亡くなっており、大きな問題となっている。非定常作業での災害が多く見られるが、大型プレスやターレットパンチプレスでの被災も多い。プレス機械により毎年死亡災害が発生していることに対して、今後も真剣に対応していかなければならない。ここにおいても機械の包括安全基準の導入がきわめて重要になることは言うまでもない。
スライドによる危険の防止だけではなく。プレスに関連する金型や材料の運搬作業から部品の搬出までの過程の中で、それぞれに安全を最後先にする考え方が重要になってくる。すぐにでもプレス機械に起因する死亡災害はゼロにしなくてはならない。安全措置の方法も構造規格に要求されるレベルから先取りした安全措置が必要である。その意味で欧州規格の導入はきわめて効果的であると思われる。
最近の安全ガード、安全装置
プレス災害の決め手はガードであるという欧州の考え方は、きわめて示唆に富む指摘であり、国際規格(|坎州規格)の中でもガードの詳細が決められている。わが国でも、ISO12100機械類の安全性を中核としてインタロックや防護方法などがJIS化されている。ISO14120、JIS B 9716「ガードー固定ガードと可動ガードの設計及び制作のための一般的要求事項」
・IS0 14119 J IS B 9710「ガードインターロック装置一設計及び選択のための一般的要求
事項」
・ISO 13852 JIS B 9707 「危険区域に上肢が到達することを防止するための安全距離」
・ISO 13853 JIS B 9708 [危険区域に下肢が到達することを防止するための安全距離」
・ISO 13854 JIS B 9708 [人体部位が押しつぶされることを回避するための最小隙問」
・ISO 14123 JIS B 9709 「機械矧から放出される危険物質による健康へのリスク低減」
などが国際安全基準として導入されつつある国際規格に準じてJIS化されたものを設備設置の最初から現場に導入することが最善であり、国際的な工場艇洲をする大企袰では必須のことである。しかしながら国内の中小企業のプレス現場では、このような国際規格を完全に導入しながらプレスの安全対策を継続することは難しい。ガードは基本中の基本だが。継統して使用できないものはかえって危険にさらしてしまうことがある。作業の性質を鑑みて第一義に行う対策は国際規格レベルのガードであることは言うまでもない。作業の内容に応じて
一つの安全対策としての完令なガードを継続的に使用できる環境があれば、この形をとることがベストである。中小企業のプレスエ場では、一台のプレスで多品種の作業を少量で生産していかなければならないので、それぞれの作業の内容に応じた安全装置・安全措置を複数に多用していかなければならない(図2)。
プレス機械や作業内容が専用化されていれば、安令措置も単一化することが可能だが、汎用化されていれば、それぞれに対応した安全措置が複数必要になる。実際にはプレス機械は汎用化されているので、安全対策は複数のものが必要になり、作業こ応じて選択して使用していかなければならない。例えば、連続打ち抜き作業専門のプレス機械であれば、固定のガードが最も安全性が高く生産性もあまり落とさないで対応できるが、大物作業、小物作業、絞り工程、曲げ工程など多様な作業を実施するなら、それぞれに応じた安全対策が必要なのである。残念ながら、現在のレベルでは、万能の安全装置は存在しない。光線式の安全装置では、二次加工の材料を保持して加工する時には支障があり、無効化して他の対策を実施しないと不可能なことがある。例えば光軸の一部を無効にする措置なども必要になってくる。安全装置として最近実用化されたものには、制御機能付光線式安令装置(PSDI)、レーザースキャナー、レーザービーム式プレスブレーキ安全検出装置などがある。
・IS0 14119 J IS B 9710「ガードインターロック装置一設計及び選択のための一般的要求
事項」
・ISO 13852 JIS B 9707 「危険区域に上肢が到達することを防止するための安全距離」
・ISO 13853 JIS B 9708 [危険区域に下肢が到達することを防止するための安全距離」
・ISO 13854 JIS B 9708 [人体部位が押しつぶされることを回避するための最小隙問」
・ISO 14123 JIS B 9709 「機械矧から放出される危険物質による健康へのリスク低減」
などが国際安全基準として導入されつつある国際規格に準じてJIS化されたものを設備設置の最初から現場に導入することが最善であり、国際的な工場艇洲をする大企袰では必須のことである。しかしながら国内の中小企業のプレス現場では、このような国際規格を完全に導入しながらプレスの安全対策を継続することは難しい。ガードは基本中の基本だが。継統して使用できないものはかえって危険にさらしてしまうことがある。作業の性質を鑑みて第一義に行う対策は国際規格レベルのガードであることは言うまでもない。作業の内容に応じて
一つの安全対策としての完令なガードを継続的に使用できる環境があれば、この形をとることがベストである。中小企業のプレスエ場では、一台のプレスで多品種の作業を少量で生産していかなければならないので、それぞれの作業の内容に応じた安全装置・安全措置を複数に多用していかなければならない(図2)。
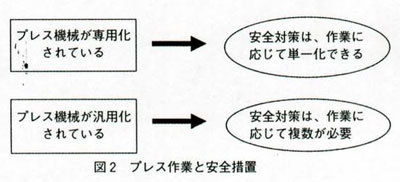
プレス機械や作業内容が専用化されていれば、安令措置も単一化することが可能だが、汎用化されていれば、それぞれに対応した安全措置が複数必要になる。実際にはプレス機械は汎用化されているので、安全対策は複数のものが必要になり、作業こ応じて選択して使用していかなければならない。例えば、連続打ち抜き作業専門のプレス機械であれば、固定のガードが最も安全性が高く生産性もあまり落とさないで対応できるが、大物作業、小物作業、絞り工程、曲げ工程など多様な作業を実施するなら、それぞれに応じた安全対策が必要なのである。残念ながら、現在のレベルでは、万能の安全装置は存在しない。光線式の安全装置では、二次加工の材料を保持して加工する時には支障があり、無効化して他の対策を実施しないと不可能なことがある。例えば光軸の一部を無効にする措置なども必要になってくる。安全装置として最近実用化されたものには、制御機能付光線式安令装置(PSDI)、レーザースキャナー、レーザービーム式プレスブレーキ安全検出装置などがある。
PSDI
PSDIは「PresenceSensing Device Initiation」の頭文字をとった英語の省略語で安全装置によって機械を起動させるシステムのことである(図3)欧州規格レベルのガードを装備、押しボタンを押す手間を省き生産性が向上するということで普及し始めている。通常の光線式安令装置は、手が危険限界に入ると機械を停止させる機能(ガードオンリー機能)だけしか持っていないが、PSDIは、これに追加して手が危険限界からなくなるとボタンを押さなくても機械を動かすことができるという起動システムを併せ持ったものである。
その効果として、単調で同じ動作をくり返す作業では、次のワークを取りに行く時にボタンを押さなくても自動的に機械が動くので、生産性が大幅に向上する。普通の手送り作業と比べて20~30%程度上がるといわれている。ボタンを押す必要がないので。作業者の疲労もかなり軽減される。安全性と生産性そして作業者の疲労軽減も図ることができる。注意事項として、意思に反して機械が動いてしまうことがあるので、使用条件についてかなり厳しく規定されている。作業領域の前面だけでなく全周囲防護(両側面、後面)が要求され、連続遮光幅など安全装置のハードウェアにも従来のものより完成度が高いものが要求されている。機械とのインタロックも強化されているので、安全装置を外して作業することはできない。
その効果として、単調で同じ動作をくり返す作業では、次のワークを取りに行く時にボタンを押さなくても自動的に機械が動くので、生産性が大幅に向上する。普通の手送り作業と比べて20~30%程度上がるといわれている。ボタンを押す必要がないので。作業者の疲労もかなり軽減される。安全性と生産性そして作業者の疲労軽減も図ることができる。注意事項として、意思に反して機械が動いてしまうことがあるので、使用条件についてかなり厳しく規定されている。作業領域の前面だけでなく全周囲防護(両側面、後面)が要求され、連続遮光幅など安全装置のハードウェアにも従来のものより完成度が高いものが要求されている。機械とのインタロックも強化されているので、安全装置を外して作業することはできない。
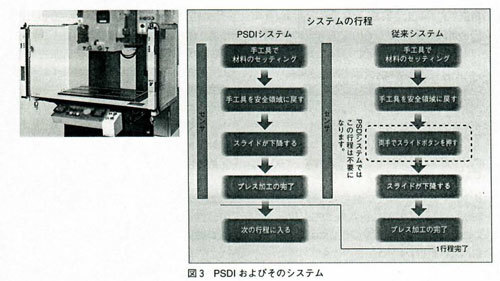
レーザースキャナー
レーザースキャナーは、一本のレーザー光線を360度スキャンさせて距離を測定し、そのうちの任意の180皮の範囲を自由な形状で検知する非常に便利な装置である(図4)。ホルスターの内部の人体検知、ムービ冫グボルスターの末端検出、ロボットの稼働領域への侵人防護などにも効果を発揮している。領域の自由設計にはパソコンを利用する
レーザービーム式プレスブレーキ安全検出装置
レーザービーム式検出装置は、光線の太い光軸とは異なり、極細のレーザー光線が微細なものを検知するので、指先の細かい動きを検知できるのが特徴である。プレスブレーキ作業の指先安全検出装置として使われている。スライドの高速加工の時点では光線式安全装置で検出し、加工する時の微加工速度の時に、このレーザービームを活用して作業を行うことができる。指の微細な動きも検知するので、光線とは異なった装置と考えられる。二次曲げには使えないことが多いが。一時曲げには効果を発抑している(図5)。
今後は、撮像素子(テレビ)を使用たパターン認識技術もプレス安全装置に応用され、技術開発にしのぎを削っている。
今後は、撮像素子(テレビ)を使用たパターン認識技術もプレス安全装置に応用され、技術開発にしのぎを削っている。
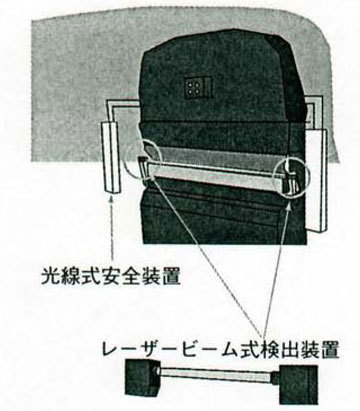
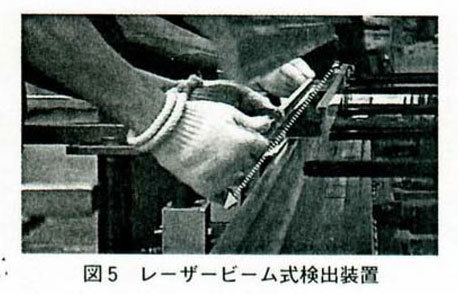
特定自主検査、点検について
概数で把握すると、国内に設置されているプレス機械は約35万台程度、そのうち18万台を検査業者が検査し、6万台を事業内検査者が実施している。70%の実施率であり、かなりの成果を納めている。プレス機械は寿命の長い機械であり、税法上の償却年限を超えて使使用するのは常識である。 40年、50年を経過したプレスも筆者はよく目にしている。このような環境の中で毎年一定の検査基準で実施することの意味は大きく、作業者が安心して作業を進めるためには必須の制度である。この制度は日本独自のもので欧州をはじめ、米国にもアジア諦国にも見られない。また、特定自主検査の検査基準は海外の規格や制度と比較しても非常に優れたものとなっている。日常点検の方法などは欧州や米国にも基準があるが、年次検査の基準として詳細な技術指針を公開しているのは日本だけである。機械を大事に使い、故障が発生した時にどこを修理するか明確になっていることが非常に重要であり、日常の不具合があった時でも対応が容易である。毎年、確実に検査することで経年変化も把握できるので重要である。検査業者による検査結果を見ると、危険防止機能についての不良が多く見られている。
安全距離の不良や取付高さの不良が55%で半数を占め、クラッチブレーキの不具合などもかなり指摘されている(表2)。 残念ながらプレス特定自主検査結果表(表3)を見ると検査業者と事業内検査では結果が異なっていることがわかる。検査業者が実施した417台のうち、合格率が5.5%であるのに対し事業内検検査者が実施した320台の結果を見ると合格率が4.7%である。検査者のおかれている立場の違いを勘案したとしても問題の残る数字である。特定自主検査は健康診断ではあるが、病気と健康の差が医師によって大きく差が出てしまうのでは、検査レベルの差があると言わざるを得ない。事業内検査者のレベルを一段と向上させなければならない。能力向上教育(中災防にて実施中)を受講し、技術レベルを上げ、適正な検査を実施して欲しいものである。
最近の動向過去10年の間、「日本の製造業は終焉を迎え、ものづくりはアジア諦国へ移っていく」と言われ、誰もがそれを信じていた。しかし、現在は、工作機械をはじめ機械工業全体は、自動車産業の好調を背景に未曾有の好況に遭遇している。プレス機械メーカーも部品製造のプレスユーザーもかなり好調である。さらに日本独自で世界に類を見ないサーボプレスも出荷が順調である。このサーボプレスの出現はプレスと工作機械の垣根を開放してしまうことも考えられている。従来まで加工速度や加工範囲を変えられなかったプレス機械が新たにフリーなモーションで加工できることが世界的に注目されているところである。サーボモータを駆動源にすることで、従来まで不可能とされていたスライドの加工速度の調整やスライドストローク長さの訓整も容易になり、加工条件をデジタルで制御できることがサーボプレスの優秀な面である。大型から小型まで様々なバリエーションが誕生している。
日本発・世界制覇も現実のものとなっている。プレスメーカー各社は技術開発に余念がない。中国では大量生産がかなりの速度で浸透し外貨をしっかり稼いでいるが、貿易収支が改善しないと言われている。なぜかと言えば、大量生産が進んでも、日本からの材料や部品も大量に輸入されているからである。中国の発展が続く限り、日本の発展も続くわけで、不況が到来するのにはたっぷりと時間がかかりそうである。このような新しい技術の開発と構造規格は、背反的な部分があるが。技術の進小に法整備が遅れることが少なくなるようにしなくてはならない。
従来のように技術的に問題がある製品には、構造規格は重要であり、検定制度が威力を発輝するが、最近のように技術開発のスピードが速くなってくると構造規格が開発を阻害する場面も出てきてしまう。昨年度報告された(社)産業安全技術協会の「構造規格の見直しの推進に関する調査報告杳」ではプレス機械構造規格・安全装置構造規格の改正案がすでに提案されている。従来までの規格は、個々の部品や製品について個別具体的な要件を細かく規定していたが、今回の提案では、性能を規格の中心に据えて個別の規定は最小限にしており、今後の技術開発を阻害しないような方式になっている。技術の進歩が’早いので、同等の性能を有するものが開発されても使えないという矛盾は回避できると思われる。早期の実現を大いに望むところである。
国際規格の対応については非常に議論のあるところだが、結論としては日本独自の環境を十分に把握し、実現可能なものを推進すべきと思う。スタンダードはダブルであってはならないが、欧州の決め方に対して簡単に全面賛成ということは難しい。筆者が本年3月に訪米し関係者との打ち合わせをした限りでは米国と欧州規格の整合は、かなりの時間を要することが明確になった。
アメリカ規格協会のD氏によれば、規格の整合のキーワードは、①ペインフルバンピーロード(痛みを伴う凸凹の道のり)、②トレメンダスミスアンダスタンディング(大変大きな誤解)、③イグザクトオポジット(ほとんどが反対の考え方)との報告だった。日本をはじめとするアジアの生産主義の中では、簡単に規格を整合することはアメリカと欧州よりも難しいと思われる。国内の事情と文化の中に溶け込んで実行できる形での応用翻訳が必要と思われる。
最近開催されたアジア諸国の安全管理担当者会議でも、日本のプレス安全水準が現場に即しているという賛辞をいただいた。現在のままでは不十分であるが、アジア規格のようなものが完成されることを望むところである。
安全距離の不良や取付高さの不良が55%で半数を占め、クラッチブレーキの不具合などもかなり指摘されている(表2)。 残念ながらプレス特定自主検査結果表(表3)を見ると検査業者と事業内検査では結果が異なっていることがわかる。検査業者が実施した417台のうち、合格率が5.5%であるのに対し事業内検検査者が実施した320台の結果を見ると合格率が4.7%である。検査者のおかれている立場の違いを勘案したとしても問題の残る数字である。特定自主検査は健康診断ではあるが、病気と健康の差が医師によって大きく差が出てしまうのでは、検査レベルの差があると言わざるを得ない。事業内検査者のレベルを一段と向上させなければならない。能力向上教育(中災防にて実施中)を受講し、技術レベルを上げ、適正な検査を実施して欲しいものである。
最近の動向過去10年の間、「日本の製造業は終焉を迎え、ものづくりはアジア諦国へ移っていく」と言われ、誰もがそれを信じていた。しかし、現在は、工作機械をはじめ機械工業全体は、自動車産業の好調を背景に未曾有の好況に遭遇している。プレス機械メーカーも部品製造のプレスユーザーもかなり好調である。さらに日本独自で世界に類を見ないサーボプレスも出荷が順調である。このサーボプレスの出現はプレスと工作機械の垣根を開放してしまうことも考えられている。従来まで加工速度や加工範囲を変えられなかったプレス機械が新たにフリーなモーションで加工できることが世界的に注目されているところである。サーボモータを駆動源にすることで、従来まで不可能とされていたスライドの加工速度の調整やスライドストローク長さの訓整も容易になり、加工条件をデジタルで制御できることがサーボプレスの優秀な面である。大型から小型まで様々なバリエーションが誕生している。
日本発・世界制覇も現実のものとなっている。プレスメーカー各社は技術開発に余念がない。中国では大量生産がかなりの速度で浸透し外貨をしっかり稼いでいるが、貿易収支が改善しないと言われている。なぜかと言えば、大量生産が進んでも、日本からの材料や部品も大量に輸入されているからである。中国の発展が続く限り、日本の発展も続くわけで、不況が到来するのにはたっぷりと時間がかかりそうである。このような新しい技術の開発と構造規格は、背反的な部分があるが。技術の進小に法整備が遅れることが少なくなるようにしなくてはならない。
従来のように技術的に問題がある製品には、構造規格は重要であり、検定制度が威力を発輝するが、最近のように技術開発のスピードが速くなってくると構造規格が開発を阻害する場面も出てきてしまう。昨年度報告された(社)産業安全技術協会の「構造規格の見直しの推進に関する調査報告杳」ではプレス機械構造規格・安全装置構造規格の改正案がすでに提案されている。従来までの規格は、個々の部品や製品について個別具体的な要件を細かく規定していたが、今回の提案では、性能を規格の中心に据えて個別の規定は最小限にしており、今後の技術開発を阻害しないような方式になっている。技術の進歩が’早いので、同等の性能を有するものが開発されても使えないという矛盾は回避できると思われる。早期の実現を大いに望むところである。
国際規格の対応については非常に議論のあるところだが、結論としては日本独自の環境を十分に把握し、実現可能なものを推進すべきと思う。スタンダードはダブルであってはならないが、欧州の決め方に対して簡単に全面賛成ということは難しい。筆者が本年3月に訪米し関係者との打ち合わせをした限りでは米国と欧州規格の整合は、かなりの時間を要することが明確になった。
アメリカ規格協会のD氏によれば、規格の整合のキーワードは、①ペインフルバンピーロード(痛みを伴う凸凹の道のり)、②トレメンダスミスアンダスタンディング(大変大きな誤解)、③イグザクトオポジット(ほとんどが反対の考え方)との報告だった。日本をはじめとするアジアの生産主義の中では、簡単に規格を整合することはアメリカと欧州よりも難しいと思われる。国内の事情と文化の中に溶け込んで実行できる形での応用翻訳が必要と思われる。
最近開催されたアジア諸国の安全管理担当者会議でも、日本のプレス安全水準が現場に即しているという賛辞をいただいた。現在のままでは不十分であるが、アジア規格のようなものが完成されることを望むところである。
今後の進め方
機械産業の好況は続くと思われるが、好況に伴つて事故が増加するのではなく、反比例して好況になるほど災害が減少するような傾向を促したいものである。これを実現するために、今後のプレスの安全対策の進め方として次のことを提案する。
①防護の概念は、プレス作業者だけでなく、関係第三者(金型設置担当者、点検・補助作業者など)も含めた形で安全対策を検討する。
②プレス機械や安全装置が故障しても必ず安全側に機能させるフェイルセーフ機能を充実させる
③リスクアセスメントを実施し。自動化システムやロボット作業でも積極的な安全対策が必要である。このリスクアセスメントを通じ、PDCAサイクルをくり返しながら徐々に危険有害要因を除去していく。
④安全対策を継続的で確実なものにするには、コスト低減・疲労軽減・生産性アップを安全対策の中に収り込んでいく。作業に応じた対策が重要である。
⑤機械の包括的な安全基準をプレス現場に積極的に導入し、機械メーカー・ユーザー・安全装置メーカーと連携し、先取りの安全対策を実施する。 (こもり まさひろ
![]() |
---|
安全と健康 |
「プレス作業の安全対策」 |